Hot Melt Roller Coater Systems
Diemme Hot-melt roller coaters are designed for the application of hot applied materials including reactive systems such as Polyurethane hot-melt and thermoplastic hot-melts.
Hot- melt rollers give a full surface coverage onto flat surfaces; the adhesive is only applied where in contact with the substrate being bonded therefore there is no waste material over the edges or through apertures in the panel.
Hot melt roller coaters are particularly advantageous in high output applications and are commonly used in conjunction with adhesive systems that allow immediate handle-ability.
- Roller Coating of flat surfaces with irregular shaped edges
- Can coat fibrous materials
- Coating edge to edge
- Uniform distribution of adhesive
- Variable coat weight
- High volume throughput
Features and Benefits - Hot Melt Roller Coater
- Hardened application roller
- Electronic temperature controller
- Variable speed
- Pneumatically operated contact pressure roller
- Pneumatically activated start with combined control of the doctor blade
- Manually operated lubrication system
|
|
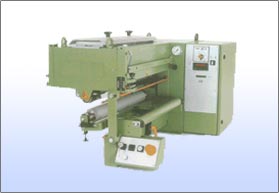 |
The roller coated uses re-circulated hot oil to heat the chromed steel "doctor" (dosing)
roller to ensure the highest accuracy in temperature control across the width of the roller and to ensure the
roller temperature is maintained. The heating system is a modular system outside of the roller coater allowing easy maintenance
or replacement should a heater element expire. For double sided roller coaters the top and bottom rollers use
independent re-circulating oil heating systems to enable maximum temperature control and flexibility.
The top rollers are housed on a special suspension system with high tension springs that allow a movement of up to
3mm across the width of the roller; this allows the system to compensate for a varying tolerance in height across the width
of the material being coated ensuring the best possible constant coating and protects both the machine mechanics
and the substrates when height tolerances vary slightly.
The silicon is coated the full width of the application roller and more than 10mm thick allowing multiple re-newing of the silicone surface and improving the insulation properties of the silicone roller to minimise heat loss.
A pneumatic operated piston drives the teflon cheek which is supported on all four sides against the roller to hold the adhesive in place. And minimise any opportunity to leak.
The system includes an external temperature sensor measuring the temperature on the surface of the silicone application roller to allow the operator to monitor the actual adhesive temperature in the roller.
A key feature to the Diemme roller coater is the PLC touch
screen control system.
The roller coater PLC is designed as the control station for
the complete line allowing the modular addition of equipment
components. The standard screen allows the addition of
various conveyors, brush panel cleaner, nip roller and drum
un-loader for which parameters such as height, temperature
and line speed can be controlled via the roller coater. Once
the parameters have been set the line speed of all the
equipment modules can be increased and decreased in a
linear way altogether using one touch screen dial.
This system can be personalised to suit the customers
requirements and updated using the USB stick connection
on the front of the PLC.
|
|
One feature utilising the systems PLC is an automatic clean function. When activated the PLC automatically adjusts the coating gap,
removes the glue, feeds the cleaner material into the roller and cycles the machine in reverse and forward for the required period of
time and for as many cycles as needed*.
*Feeding tank for cleaner & motorised doctor rollers an optional extra.
The added versatility the PLC control system provides potentially labour reducing benefits along with a controlled
repeat-ability for processes such as cleaning that will ultimately protect the application roller life.
To ensure a constant adhesive level in the roller during use the machine uses a Siemens level sensor that via the PLC activates
pneumatic switches to operate the application guns and a relay to inform the adhesive melting unit pump to start.
The PLC can use the data to control the period of time the machine pumps adhesive into the roller after receiving a low
level signal from the sensor, this helps prevent excessive triggering of the guns reducing needless wear on the equipment.
On the inlet side of the roller there is a protection bar to stop the roller drives should an over sized panel be place into the roller.
For additional operator safety there are kick bars on the in feed and out feed of the roller along with an emergency hit switch on the
control panel that will automatically stop the rollers turning, by simply pressing the reset they rollers will start again.
When the doors are opened the rollers automatically stop and restart again automatically when closed.
Each roller is "direct drive" and controllable via the PLC allowing maximum control of the machine and long term accuracy.
Motorised height adjustment is standard, to motorise the doctor roller movement is an optional extra.
The motors are housed outside of the heated roller zone to protect them both from heat exposure and out gassing of the adhesive.
|